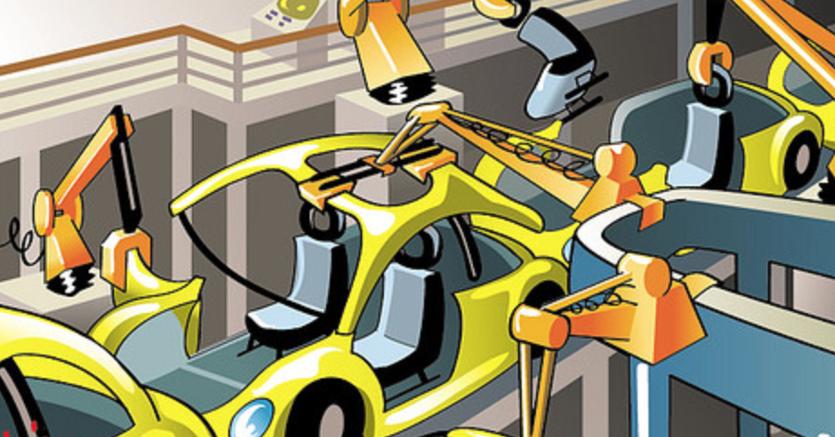
La quarta rivoluzione industriale è sinonimo di digitalizzazione delle fabbriche o anche altro? Il modello tedesco di Industry 4.0 è da copiare in Italia oppure no? Molti addetti ai lavori sono concordi nel ritenere necessaria una strategia condivisa a livello di sistema Paese: ma dove (e come) le aziende italiane devono intervenire per cambiare passo sfruttando i benefici delle nuove tecnologie? Domande che animano da tempo la discussione che ruota intorno al tema del “digital manufacturing”, divenuto centrale anche nelle politiche di sviluppo per l'innovazione a livello di Commissione europea. Domande che Nòva ha rivolto a Marco Taisch, Professor of Advanced & Sustainable Manufacturing and Operations Management del Politecnico di Milano nonché Scientific Chairman del World Manufacturing Forum edizione 2016 che si è tenuta a Barcellona il 3 e 4 maggio. Un evento che chiama a raccolta oltre 400 esperti della materia fra rappresentanti delle istituzioni, analisti e industria privata e che, questo l'auspicio, potrebbe trovare in futuro fissa dimora a Milano.
«Dai tedeschi – esordisce così Taisch – possiamo sicuramente prendere esempio ma dobbiamo anche adottare un modello italiano. La strategia sulla carta c'è ma va implementata, tirata fuori dai cassetti e condivisa fra tutti gli stakeholder coinvolti. Il grande valore di Industry 4.0 è la popolarità di questo progetto, il fatto che sia riconosciuto come modello. Eppure sono passati quattro anni da quando è stato lanciato. La tecnologia intanto è andata avanti e la sua adozione si limita sostanzialmente a una parte dell'industria tedesca, grandi fornitori di automazione in primis».
L'Italia, insomma, deve poter muoversi con le proprie gambe, anche perché – doveroso ricordarlo – è sempre il secondo Paese europeo nel campo della produzione di macchine utensili. E deve capire, secondo Taisch, che la rivoluzione cui è chiamato il mondo manifatturiero non è solo Industry 4.0, e quindi la digitalizzazione delle varie anime della fabbrica. È anche servitizzazione (e quindi il passaggio dalla logica di prodotto a quella di servizio), è economia circolare, è l'adozione di tecnologie per la gestione dell'intero ciclo di vita del prodotto/servizio.
«Il digitale è un elemento necessario ma non sufficiente», spiega ancora l'esperto. E si parla quindi di «circular manufacturing», di un paradigma che associa nuovi modelli di business e tecnologici al principio di una logistica di ritorno per la gestione degli scarti di produzione. La strategia per arrivare al nuovo manifatturiero, insomma, si ispira a una visione ben definita: «la quarta rivoluzione industriale è la presa di consapevolezza della possibilità di utilizzare le tecnologie digitali per migliorare i processi». Ha quindi senso parlare di fabbrica aumentata, di trasformazione legata all'adozione dei sistemi di “additive manufacturing” (con l'utilizzo delle stampanti 3D) ma non va dimenticato come i servizi collegati al manifatturiero, estesi a tutta la catena del valore, abbiano talvolta una dimensione economica superiore a quella della produzione stessa, incidendo sensibilmente sul Pil. Il cambiamento che predica Industry 4.0, insomma, si gioca su più piani e non solo a livello di linee di assemblaggio.
L'innovazione incrementale delle piccole imprese
La consapevolezza di poter cambiare marcia manca ancora soprattutto alle piccole e medie imprese, a cui è riservata però un'opportunità che il professore del Politecnico definisce, letteralmente, “incredibile”. Quale? Quella di poter fare innovazione passo dopo passo in modo incrementale, sfruttando strumenti come le app da integrare sulle macchine o i servizi cloud per la progettazione o le tecnologie dell'Internet of Things. Il rischio di non coglierla, questa opportunità, però c'è e si materializza (spesso) nella mancanza di competenze e di risorse. E avrebbe come effetto, a detta di Taisch, «l'aumento del gap delle Pmi verso le grandi imprese. Per questo deve crescere la consapevolezza fra tutti gli attori coinvolti attraverso un allineamento sinergico fra pubblico e privato, mondo della ricerca, istituzioni e imprenditoria».
Dentro le aziende, invece, dovrebbe prendere piede un processo di trasformazione ispirato al principio dell'automazione cognitiva, e cioè il passaggio da un modello di automazione di fabbrica in cui i robot sostituiscono le persone a un modello in cui circolano maggiori informazioni contestualizzate, precise e in tempo reale. L'esempio cui ricorre il professore per spiegare questo concetto è facilmente decifrabile: un addetto munito di tablet o smartphone migliora la propria operatività e rimane centrale nel processo industriale perché i dati lo rendono più intelligente. Sensorizzare attraverso l'Internet delle cose e l'intelligenza artificiale l'esperienza e l'abilità del lavoratore con più esperienza e know how, facendo di questo una sorta di maestro aumentato delle best practice di fabbrica, è il passo successivo (e al momento solo futuribile per molte imprese manifatturiere) a quello di sensorizzare le macchine utensili, i reparti e i magazzini per avere una situazione in real time degli impianti e per fare manutenzione preventiva degli stessi. Per abbracciare la nuova rivoluzione industriale si deve quindi partire, conclude Taisch, «dal digitalizzare in modo sistemico e strutturato il mondo fisico, creando un avatar di questo mondo e collegamenti sempre attivi fra il sistema informativo centrale dell'azienda e i sistemi Erp che gestiscono la produzione. Non servono investimenti colossali ma poche decine di migliaia di euro diluite nel tempo».
© Riproduzione riservata