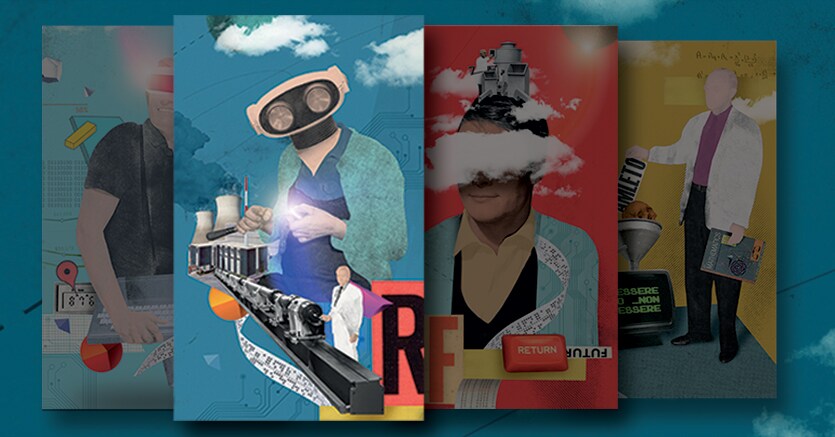
La fabbrica lavora in silenzio. Chi ricorda il frastuono degli stabilimenti del secolo scorso scopre che le esternalità negative misurate in decibel sono finite. Nella campata centrale dello stabilimento i robot piegano, bucano, assemblano pezzi d’acciaio, mentre le persone si aggirano tra i passaggi segnati dalle strisce gialle per controllare ogni aspetto della produzione sui tablet o sui computer appollaiati sulle grate che separano le macchine dagli umani. Quegli schermi sono le sole finestre sulla fitta rete invisibile di informazioni che avvolge tutto, alimentata da persone, sensori ed elaboratori in cloud. Gli operai e i tecnici sono prevalentemente giovani, tatuati, in forma nella loro attillata t-shirt aziendale nera, peraltro non obbligatoria. In generale, l’età media nell’impianto è sui 35 anni, ma i nuovi assunti hanno mediamente 24 anni. E sono tanti. Perché l’azienda fatturava 25 milioni nel 2012 e oggi è arrivata a 100 milioni. Siamo a Salvaterra di Reggio Emilia, circondati dalla campagna industrializzata del distretto della ceramica vicino a Sassuolo. Qui, alla Modula, si costruiscono i magazzini verticali, armadi automatizzati alti anche 14 metri. I Modula consentono di immagazzinare e raggiungere gli oggetti in modo efficiente, tracciare ogni movimento dei pezzi, ridurre fino al 90% lo spazio occupato a terra. La generazione di dati e la loro valorizzazione è la frontiera. Per questo, mentre i robot si moltiplicano, si assumono nuove figure come business analyst e data scientist. Del resto, vendita e produzione sono strettamente collegate: il configuratore aiuta il cliente a scegliere la sua macchina e manda l’ordine alla fabbrica che inizia a realizzarla, spiega Massimiliano Gigli, direttore commerciale internazionale, con Alice Belleli del marketing. Ogni gesto, umano o robotico, è tracciato in modo sempre meno casuale. La rete di informazioni che anima l’azienda è pensata in ogni dettaglio da giovani ingegneri gestionali, come Pamela Catrambona e Federica Mosto. Ed è compresa la formazione, diventata parte integrante dell’attività produttiva. I “learning objects” sono prodotti in casa e fruiti su piattaforme leggere come Docebo, Videoscribe, GoAnimate. Modula è parte di System Group, fondata dal mitico Franco Stefani, startupper degli anni Settanta del Novecento, che ormai guida un gruppo da 440 milioni di fatturato e 2mila persone, aumentate ancora l’anno scorso di 300 unità. Anche perché non si limita a fare macchine per la ceramica: inventa nuovi mercati, come quello delle sottilissime lastre di ceramica di ampia superficie che hanno portato quel materiale a fare da piano di lavoro per le cucine o rivestimento per edifici che libera la fantasia degli architetti.
Già. Operai giovani. Ingegneri impegnati. Sistemi organizzativi decentrati. Connessioni ubique. Anche il viaggio di Annalisa Magone e Tatiana Mazali nella quarta rivoluzione industriale, raccontato nel libro pubblicato per Guerini e intitolato Industria 4.0. Uomini e macchine nella fabbrica digitale, stupisce chi ricordi le fabbriche del Novecento. Raccontano di stabilimenti disegnati da architetti, popolati da giovani, organizzati intorno alla logica digitale per produrre con macchine totalmente connesse. Raccontano di Comau, Pirelli, Avio Aero, Ferrari, Ducati e molto altro. Ma non possono non fermarsi ad Agrate, alla Stm, dove i concetti dell’Industria 4.0 si applicano e si abilitano. La sensoristica, della quale il gigante della microelettronica Stm è uno dei leader mondiali, è diventata un elemento centrale dell’Industria 4.0. Lucio Colombo è responsabile degli stabilimenti di Agrate. Matteo Lo Presti è il responsabile dei business collegati all’Industria 4.0 e conosce tutti i clienti che fanno automazione.
Ricorda Colombo: «Un tempo, pensavamo le macchine una alla volta. Ogni lavoratore aveva un lotto da produrre e lo faceva con quella macchina. Oggi tutte le macchine, pur venendo da fornitori diversi, pensate come un insieme e gestite da un solo computer: che dice al lavoratore quale lotto va processato e su quale macchina, scarica le specifiche e le corrette priorità, controlla e registra le operazioni, raccoglie statistiche». E Lo Presti aggiunge: «Prima partivamo dalla fabbrica e dall’operatore. Oggi partiamo dalla domanda del cliente, aggiornata quotidianamente. Le linee di produzione sono attrezzate per seguire le richieste del mercato: non solo per la rapidità, ma anche per offrire servizio e qualità migliore». Nasce uno spazio interaziendale che collega le diverse fabbriche, i diversi fornitori e clienti: è uno spazio digitale. «Le attività di pianificazione sono diventate più importanti», dice Colombo. E Lo Presti: «Sì, occorrono ingegneri gestionali, data scientist, informatici, matematici. E poi non gli operai di dieci anni fa: servono specializzazioni e flessibilità. Sembra un ossimoro. Come ci si prepara? Un’ampia cultura di base serve alle mutevoli condizioni del lavoro». Per Colombo: «È importante seguire l’evoluzione tecnologica in modo interdisciplinare, con buone conoscenze di fondo». E Lo Presti: «Sposteremo risorse verso programmazione e progettazione che facciano lavorare le linee di produzione in modo coerente con la veloce mutazione di domanda e prodotto. Questo aumenta l’occupazione distribuendola in maniera diversa. I robot non portano via il lavoro: lo cambiano. I Paesi con più robot, Corea e Germania, sono quelli con la disoccupazione più bassa». Insomma. Non è la tecnologia che porta via il lavoro ma casomai la mancanza di innovazione tecnologica che non consente di tenere il passo con il resto del mondo e fa perdere quote di mercato e occupazione.
Ma tutto questo va compreso. Da parte di tutti. Chi lavora, chi si prepara a lavorare e chi intraprende. Una cultura aziendale omogenea, orientata al progetto comune, è una condizione fondamentale. La Luxottica coltiva questa cultura. È una multinazionale da 9 miliardi di fatturato e 80mila dipendenti nel mondo, di cui oltre 10mila in Italia. Ce ne sono 4mila ad Agordo: sono tantissimi, ma il vicepresidente Luigi Francavilla li conosce uno per uno, o quasi. Lo stabilimento di Agordo è gigantesco, complesso come la sua storia, grande quasi come il paese dall’altra parte della valle, circondato da immense montagne: la connessione globale e la tradizione locale si traducono in una interpretazione speciale dell’innovazione, con l’automazione che avanza a grandi passi mentre l’occupazione non diminuisce. Il che si spiega considerando la tecnologia, l’economia, la società che costituiscono questa impresa: «Il fine è mantenere la forza lavoro aguzzando l’ingegno», spiega Massimo Vian, amministratore delegato prodotto e operations: «Non esiste nessun incentivo per i manager che sia collegato con la riduzione dell’occupazione. Si mantiene l’occupazione solo riqualificando il lavoro. I robot triplicano la produttività, ma gli umani rispondono ad altre esigenze non automatizzabili che riguardano la varietà, diversità, creatività dei nostri prodotti».
Chi voglia entrare nel merito può partire da alcuni fatti: la Luxottica produce 93 milioni di montature da vista e occhiali da sole all’anno. Ogni anno introduce 2mila nuovi modelli, realizzati in diversi calibri e colori, per un totale di 20mila referenze, tutto compreso. I modelli evergreen sono prodotti anche in 5 milioni di pezzi all’anno, mentre di altri modelli legati a particolari occasioni si fanno anche soltanto 50 pezzi. In media, ogni modello è fatto in 4mila “copie”. Ma ciascuno di questi prodotti deve generare valore. Ci vuole una cultura del lavoro e dell’automazione particolare. Che non deve limitare la creatività. Perché tutto parte dai prodotti. Gli oltre 20 marchi in portafoglio sviluppano soluzioni estetiche, funzionali e tecnologiche diverse. L’efficienza richiede che dalla concezione al negozio non passino più di venti settimane. Si parte dalla concezione di ogni modello: che è discusso con gli stilisti, renderizzato al computer, prototipato con le macchine per la produzione additiva e rifinito dagli artigiani; si fanno le prove dei materiali, si affina il marketing connesso agli eventi (sportivi, fashion, festività), si raccolgono i dati; si fa il progetto operativo; si va in stabilimento dove operai e robot lavorano fianco a fianco. I robot in molti casi, con braccia meccaniche e vista elettronica, fanno i gesti che prima erano degli operai, spesso con gli stessi strumenti. Imparano dagli umani che intanto fanno altro, dal controllo della qualità alle rifiniture, all’ideazione incessante di miglioramenti. Intanto, i modelli fatti in piccoli numeri sono presi in carico da artigiani che usano laser, produzione additiva e vecchi strumenti manuali per venire a capo di oggetti che andranno sul mercato anche a 5mila euro l’uno. Alla fine i prodotti partono in aereo per raggiungere tutti i mercati. E i computer centrali, alimentati anche dal machine learning, cercano di prevedere le necessità di rimpiazzo dei modelli che si trovano nei 150mila negozi oppure nei siti di ecommerce. Intanto, chip rfid servono a controllare i movimenti dei prodotti per combattere la contraffazione e il mercato parallelo. Luxottica è verticalmente integrata per non perdere una goccia del valore aggiunto di questo percorso, ma anche per non perdere un momento nel quale si può migliorare la qualità del risultato finale. La formazione che serve per tutto questo? Visione internazionale, ingegneria gestionale e meccanica, programmazione di robot, design, ma non solo: «Serve saper fare squadra, usare il pensiero laterale, comunicare» dice Giorgio Striano, capo delle Operations. Per Vian è una necessità operativa: «L’automazione di piccole serie chiede un’organizzazione votata a fare scala e personalizzazione, flessibilità e velocità». Tutto questo è speciale nel mondo e forse è normale in Italia. «Facciamo valore aggiunto in piccole nicchie. Non facciamo sistema, forse, ma abbiamo il nostro sistema». Sembra una sintesi di caratteri italiani fondamentali. Ma di un’Italia che supera se stessa.
© Riproduzione riservata