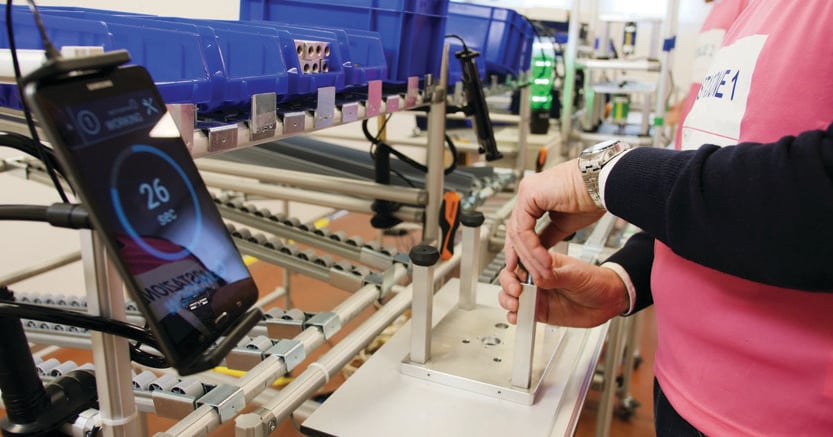
Grisignano di Zocco (Vi) - La minifabbrica è una linea di produzione che sembra uscita da un gioco di ruolo. È lunga poco più di sette metri e larga poco più di due e ha quattro postazioni di lavoro e una di controllo. Riproduce però fedelmente uno stabilimento in cui alla Lean production sono state aggiunte tecnologie e competenze 4.0. Siamo a dieci chilometri da Vicenza, nell’area industriale di Grisignano di Zocco, nella sede di Considi, partner italiano esclusivo della Toyota Academy.
La minifabbrica, tecnicamente Gear Factory, è la palestra in cui le imprese vengono istruite e addestrate all’innovazione di processo basata sul metodo lean e le tecnologie di Industria 4.0.
La Gear factory ha eliminato i reparti, i carrelli, i movimenti inutili di pezzi. Ha pulito i percorsi e cancellato gli sprechi, ridotto i tempi e annullato gli intervalli, come in una perfetta fabbrica che adotta la Lean o il Wcm (World class manufacturing) o uno degli altri sistemi di razionalizzazione dei processi che discendono dal metodo Toyota. Una fabbrica prototipo funzionale allo scopo di teoria ed esercizio. «Il 70-80% delle imprese italiane – dice il presidente di Considi Fabio Cappellozza, un ingegnere elettronico pacioso e concreto – è ancora organizzato con i reparti e le isole di produzione. Un sistema irrazionale che produce diseconomie».
Lo vediamo nello stanzone antistante alla minifabbrica. I giovani del master in gestione aziendale del Cuoa, la scuola di alta specializzazione di Altavilla Vicentina, sono alle prese con una simulazione di produzione tradizionale. Si sono mossi in uno sciamare confuso, con carrelli che si incrociano e pezzi che mancano, tra reparti e isole di lavoro. Alla fine del percorso stanno facendo i conti delle diseconomie. Oggi hanno perso settemila euro.
Il passaggio alla Lean cancellerà le perdite. Nelle postazioni della linea digitalizzata è iniziata la produzione di motori elettrici. Dalla postazione di coordinamento il caporeparto controlla su un grande schermo il magazzino e la linea. Su un tablet fa l’ordine dei pezzi dal magazzino. Sulla vaschetta che arriva nella postazione 1 c’è un’etichetta con il codice a barre di identificazione. Sul tablet dell’operatore il tempo, trenta secondi, per avviare la prima operazione e un semaforo verde, la segnalazione che la postazione 2 sta aspettando il pezzo. «Le indicazioni – dice Cappellozza – sono molto semplici: il tempo per fare l’operazione; il verde, il giallo e il rosso per la qualità dell’intervento; la situazione della postazione successiva».
Verde. Il pezzo passa alla postazione 2 nei trenta secondi previsti. Via libera allo step successivo. Trenta secondi. Verde, il pezzo scorre. Alla 3 l’operatore ha un problema. Il tempo va oltre i trenta secondi, il semaforo del tablet è rosso. L’operatore chiede l’intervento dal dispositivo. Il caporeparto riceve l’alert sull’orologio. Legge e invia un codice che appare al tablet della postazione. Si apre una schermata che dà due alternative: aprire un Pdf o guardare un video per risolvere il problema. L’operatore apre il Pdf. Deve avvitare meglio. Fatto, si va avanti. «Nelle fabbriche tradizionali – dice Cappellozza – le postazioni sono piene di cartelloni e codici che identificano le operazioni. In uno stabilimento abbiamo tagliato i codici di intervento da tremila a nove, tutti digitalizzati».
La linea va. Terza e quarta postazione senza intoppi. Lavoro finito. L’adesivo della vaschetta finisce su una lavagna fisica. Il flusso continua. Assistiamo al giro della produzione più volte. La postazione con il caporeparto fa gli ordini. Sulla linea arriva la vaschetta con l’adesivo e il codice a barre. Postazione. Tempo. Semaforo verde. Prodotto finito. Adesivo sulla lavagna. Vaschetta con adesivo. Postazione. Semaforo. Prodotto finito. Adesivo sulla lavagna. Al terzo prodotto, il collaudo e l’aggiornamento del grande display luminoso che aggiorna in diretta il lavoro: i tempi, l’indice di produttività della postazione, della linea, del magazzino e dello stabilimento. L’indice Oee, lo standard internazionale per misurare l’efficienza.
«Uno stabilimento che adotta la Lean – dice Cappellozza – può aumentare l’efficienza fino al 50%. Se si aggiunge la digitalizzazione c’è un ulteriore guadagno di margine fino al 30%. I dati sottostanti vengono immagazzinati e incrociati dai manager per le decisioni strategiche».
Cappellozza racconta di un’impresa dell’automotive che ha capito di perdere efficienza con l’aumento dell’umidità nello stabilimento. Problema risolto con un telecomando per aprire i finestroni. Scartata la soluzione standard di incapsulare la linea che sarebbe stata molto più costosa e avrebbe peggiorato la qualità della vita dei lavoratori.
«La digitalizzazione – dice Cappellozza – è il termometro che rileva il dato, fornisce le informazioni e ci consente di indirizzare gli eventi sulla linea di produzione in tempo reale. Prima di Industria 4.0 servivano almeno due giorni per intervenire. Oggi l’intervento è immediato. Non servono investimenti faraonici, va cambiata l’organizzazione e la mentalità. Lo possono fare tutte le imprese con almeno 50 dipendenti e un fatturato intorno ai 15 milioni. Le competenze dei dipendenti possono essere implementate facilmente: sono gli stessi gesti che facciamo tutti i giorni sui nostri smartphone».
Padova, pochi chilometri a Est di Grisignano. Stabilimento di hGears, multinazionale tascabile controllata dal fondo Finatem in cui sono confluite la tedesca Herzog e la padovana mG dal gruppo Carraro. Tre stabilimenti: Padova, Lauterbach (in Germania, nella Foresta Nera) e Suzhou (Cina). hGears produce componentistica e ingranaggi in acciaio per l’automotive, le macchine utensili, l’ebike e il giardinaggio. È fornitore, tra gli altri, di Audi, Bmw, Ferrari, Bosch, Porsche. Mille dipendenti, 140 milioni di fatturato, 7% dei ricavi investiti in conto capitale, 3% in ricerca, 15mila ore di formazione all’anno.
Federico Mangolini è il direttore operativo del gruppo e responsabile dello stabilimento di Padova, 17mila metri quadrati. Ferrarese, 50 anni, è un ingegnere aerospaziale con il pallino dell’innovazione di processo e della digitalizzazione. «Abbiamo iniziato a lavorare a un progetto di completa trasformazione del gruppo nel 2017. Nel 2021 – dice – contiamo di arrivare a implementare Lean e tecnologie 4.0 nei tre stabilimenti. Ma è un lavoro che va fatto con pazienza, giorno per giorno, coinvolgendo i dipendenti, vincendo le loro ritrosie. La perfezione di Industria 4.0 esiste solo nelle slide dei convegni e anche in Germania c’è ancora moltissima strada da fare».
Alla hGears hanno scelto i passi calibrati. Messa in linea e digitalizzazione dello stabilimento a tranche, introduzione immediata del controllo remoto della produzione da parte degli operai. «Abbiamo eliminato la carta e i report. Introdotto tablet, sensori e orologi. Quando abbiamo detto agli operai che nel weekend potevano fare le operazioni di intervento da casa ci hanno guardato increduli. Li abbiamo dovuti convincere», racconta Mangolini. La riorganizzazione, nel 2017, ha portato a un incremento della produzione in valore del 13%, da 180mila a 210mila euro al giorno. «Tutti i dipendenti, dall’usciere all’amministratore delegato, ricevono la foto del report giornaliero. Le informazioni devono circolare – dice Mangolini – senza la collaborazione di tutti non si va lontano».
Nello stabilimento le aree in cui ci sono stati gli interventi si vedono a occhio nudo. Pulite, luminose, gli operai davanti ai tablet, i robot in azione. Nell’area finitura, in cui si preparano componenti per la Audi, gli operai non toccano i pezzi dall’ingresso in linea all’uscita del prodotto finito. L’investimento sulla linea è stato di 1,5 milioni. Gli addetti da nove diventeranno sei. «Ma la produttività è aumentata e i dipendenti sono passati da 280 a 291», dice Mangolini mentre apre la porta della sala di controllo. C’è una grande lavagna in cui i capireparto nei tre briefing - alle 9, alle 12 e alle 17 -, segnano l’andamento della produzione e l’indice Oee ripreso dal grande display digitale collegato alle linee. L’anno scorso è stato del 74,5%, livelli quasi giapponesi. Oggi è al 59%. «Basso. In questo periodo abbiamo avuto molte assenze per influenza che hanno rallentato i ritmi. Ma non è solo questo, lo sappiamo bene dai dati e stiamo preparando un intervento più strutturale», dice Mangolini.
Prima di uscire dallo stabilimento entriamo nell’area della linea che produce la Power tech unit della Ferrari. Qui le informazioni sono condivise anche con il cliente. In qualsiasi momento della produzione di ogni singolo pezzo Ferrari può accedere ai dati di lavorazione. Anche anni dopo. Anche in caso di un improbabile guasto. Basta un clic da Maranello.
© Riproduzione riservata