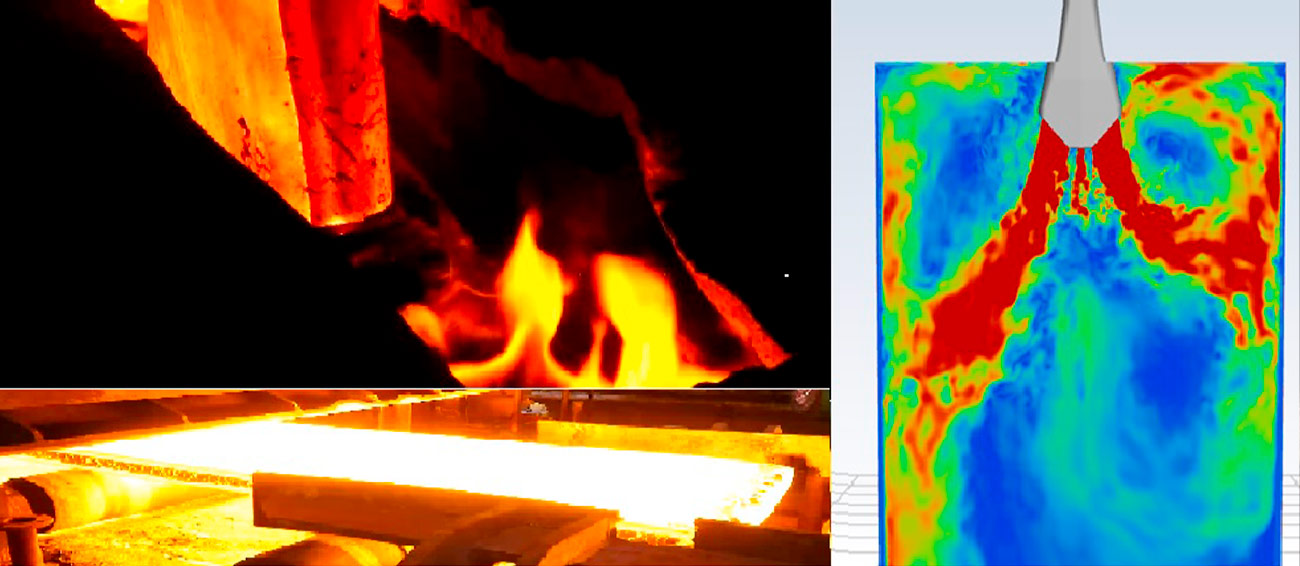
D-SIM, un gemello digitale alla ricerca della “colata perfetta” per il settore automotive
Realizzare un gemello digitale della colata d’acciaio, in grado di prevenire la creazione di difetti e di ottenere così un prodotto di qualità adatto alle esigenze del settore automotive, riducendo la quantità di scarti in produzione. È questo, in sintesi, l’obiettivo del progetto D-SIM, acronimo di Digital Slag Infiltration Model, finanziato dall’Unione Europea (NextGenerationEU) all'interno dell'ecosistema dell'innovazione iNEST (Interconnected Nord-Est Innovation Ecosystem) nell’ambito delle attività dello Spoke 9 – Models, Methods, Computing Technologies for Digital Twin, guidato dalla Scuola Internazionale Superiore di Studi Avanzati (SISSA) di Trieste. Capofila del progetto è Danieli & C. Officine Meccaniche SPA, gruppo friulano che nel 2024 ha registrato un fatturato di 4,3 miliardi di euro e conta circa 10mila dipendenti in tutto il mondo e una forte presenza internazionale.
Il digital twin, sviluppato al Danieli Research Center di Buttrio (Udine), è in sostanza una replica virtuale di un processo industriale nell’ambito della siderurgia, e in particolare nella produzione destinata al mercato automotive. «Abbiamo dei laminati che poi vengono utilizzati per le carrozzerie delle automobili – spiega Lorenzo Gigli, ricercatore presso il Danieli Research Center –, per i quali occorre ottenere una qualità perfetta del prodotto finale, riducendo al massimo gli scarti. Come possiamo migliorare il processo e la qualità dei materiali? Si interviene sul processo che porta l'acciaio liquido a temperature oltre i 1500 gradi centigradi, fino alla creazione del semilavorato. Particolarmente critica, in questo contesto, è la dinamica di prima solidificazione dell'acciaio, ovvero quello che succede nel primo metro di processo, in un impianto che può avere dimensioni anche di centinaia di metri».
In termini tecnici, il progetto proposto mira a esplorare le dinamiche della prima solidificazione in lingottiera attraverso lo sviluppo di un modello matematico termo-fluidodinamico. Questo modello è stato sviluppato tramite simulazioni esplicite delle geometrie utilizzate negli impianti di produzione di bramme sottili. L’obiettivo è usare questi modelli per l’impostazione di un Digital Twin del processo di colata in lingottiera, che possa offrire nuovi strumenti per investigare la difettosità superficiale degli acciai in bramma sottile e favorire un miglioramento nel controllo del processo di colata continua ad elevata produttività.
Il Digital Twin offre inoltre la possibilità di ottenere un elevato grado di dettaglio nell’analisi della prima solidificazione dell’acciaio, permettendo di ottenere risultati numerici in condizioni operative dove tipicamente le elevate temperature, la presenza di polveri e vapore, limitano l’utilizzo di strumenti di misura.
«Se fino ad oggi Danieli ha realizzato dei modelli per descrivere i singoli fenomeni all'interno del processo produttivo – prosegue Lorenzo Gigli –, ora per la prima volta si cerca di integrare tutti gli aspetti della colata continua, che sono sostanzialmente tre: l'effetto del raffreddamento a cui è soggetto l'acciaio liquido, l'effetto dei dispositivi elettromagnetici che tendono a uniformare le temperature all'interno dell'impianto all'interno della macchina, e infine la fluidodinamica dell'acciaio liquido stesso, fondamentale per la qualità del prodotto».
Lo sviluppo del progetto si articola in una sequenza di fasi: una prima elaborazione del gemello digitale attraverso una revisione dello stato dell'arte, per comprendere quali sono le tecniche più idonee a questo scopo; il secondo step consiste nella realizzazione vera e propria del modello fluidodinamico e l'integrazione di tutti gli aspetti della colata in un unico modello; infine, la terza fase è rappresentata dalla validazione del gemello digitale, attraverso l'acquisizione sistematica di dati di impianto per un anno intero di produzione e per un impianto target. Ciò è stato possibile anche tramite tecniche di machine learning e computer vision.
Numerosi i vantaggi attesi dal progetto D-SIM. «Tramite il digital twin è stato possibile per la prima volta effettuare un'indagine molto accurata della fisica dell'impianto e correlare in modo diretto le condizioni della macchina con la difettosità e la qualità del prodotto finale – spiega Gigli –. Riusciremo, ottenendo un miglior controllo del processo di colata continua, ad aumentare gli standard di qualità degli impianti Danieli, rispondendo quindi alle esigenze sempre più pressanti da parte del settore automotive, che richiede un’elevata produttività accanto a una maggiore efficienza e a una riduzione sempre maggiore degli scarti».