Storia dell'articolo
Chiudi
Questo articolo è stato pubblicato il 07 marzo 2013 alle ore 06:41.
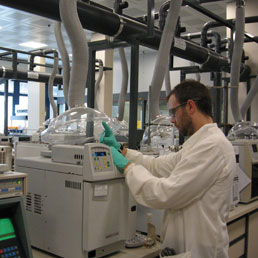
C'è la ricerca chimica made in Ferrara dietro al pacco di maccheroni, al flacone di detersivo e a decine di oggetti di uso quotidiano in polipropilene – materia plastica tra le più resistenti, leggere e plasmabili - che circondano noi e i consumatori di tutto il planisfero. Così come nascono nei laboratori estensi gli scarponi da sci di ultima generazione, i campi di erba sintetica degli stadi, i paraurti delle supercar.
Perché da oltre cinquant'anni la città estense è la culla del più importante centro ricerche al mondo sulle poliolefine (la famiglia è quella degli idrocarburi) e sui catalizzatori (gli acceleratori delle reazioni chimiche), ovvero gli ingredienti base di un'infinità di materiali e di industrie, dall'alimentare al medicale, dal tessile agli elettrodomestici fino all'automotive: il centro dedicato al premio Nobel Giulio Natta, che nel 1954 inventò il polipropilene isotattico (con gruppi di carbonio e idrogeno tutti disposti in ordine così da rendere il polimero duttile e funzionale) e di cui Ferrara divenne, tre anni dopo, il primo polo produttivo al mondo.
Ancora oggi nel mezzo della pianura bonificata dal regime fascista batte, all'interno del pentagono petrolchimico di 250 ettari e 2mila dipendenti, questo cuore pensante di 15 ettari e 500 ricercatori targato LyondellBasell (ma prima è stato Montecatini, Montedison, Montepolimeri, Himont, Montell, Basell), che sforna una cinquantina di brevetti l'anno e permette il 40% della produzione mondiale di polipropilene, attraverso la tecnologia dei catalizzatori Ziegler-Natta, la polvere magica delle reazioni di polimerizzazione che il colosso chimico americano – 45 miliardi di dollari di fatturato e 13mila dipendenti, di cui 1.000 nel sito estense – produce solo a Ferrara, in tre impianti, per tutto il mondo. Eppure mezzo secolo di storia non è bastato a costruire, attorno a questa culla d'eccellenza internazionale, un territorio prolifico di innovazione e spin-off nel settore. Al fianco di LyondellBasell ci sono altre multinazionali chimiche come Versalis (Eni) e Yara, ma non c'è stato alcun processo di gemmazione di imprese satelliti. Brevetti e brainstorming restano dentro i confini "stranieri" del petrolchimico, mentre la provincia di Ferrara langue al penultimo posto in regione per numero di brevetti o al 56° posto in Italia per opportunità di business, nonostante i record di attrattività e di produzioni scientifiche dell'ateneo estense, ma che hanno impatto economico locale irrilevante.
«In un mercato italiano, più che europeo, in forte contrazione, senza materie prime, costi energetici proibitivi e spese di trasporto rilevanti restiamo perché un centro ricerche completo non si inventa dal nulla». Così Massimo Covezzi, senior vicepresident LyondellBasell e capo dell'R&D del gigante chimico spiega perché Ferrara resterà il polo per la ricerca più importante al mondo per il gruppo, anche dopo l'annunciata e temuta cura dimagrante: si parla di un taglio del 25% del budget, da 47 a 36 milioni, e di 105 ricercatori in meno sui 476 attuali, per la riduzione dello sviluppo prodotti, attività che ha ormai basso valore aggiunto. «Si può costruire ex novo un centro sviluppo applicazioni in India o in Cina – spiega Covezzi, laurea in Ingegneria chimica a Bologna (a Ferrara c'è solo la facoltà di Chimica del corso di laurea in Scienze) e una carriera tutta interna iniziata a Ferrara nel 1984 – dove i consumi di polipropilene sono di 5 kg pro capite l'anno contro i 20 in Italia e la crisi della chimica non si sente, ma non avrebbe senso economico ricreare altrove un polo come questo».
Ovvero una cittadella di laboratori e impianti pilota che vale centinaia di milioni di euro, attraversata da competenze tecniche multiple e interconnesse, dal fisico al chimico all'ingegnere, impegnati in un dialogo continuo e integrato tra ricerca di base, tecnologie di processi e produzione finale. Per farsi un'idea della non replicabilità di questo centro, basta dare un'occhiata agli otto impianti pilota open air o al laboratorio "test catalizzatori", dove 18 piccoli reattori controllati da centraline (che rivestono intere pareti) lavorano 16 ore al giorno per sperimentare su scala ciò che avviene negli impianti industriali e verificare la qualità di ogni granello di sabbia (i catalizzatori) e di ogni perla semitrasparente di polipropilene.
Perle, anche le più preziose, che valgono meno di due euro al kg ma sono in grado di trasformarsi in pochi istanti – e si vede dal vivo nell'area processing del laboratorio – in pellicole sottilissime (per imbustare di tutto, dalle merendine alla pasta), in bicchieri di plastica, in filati hi-tech. Qualche edificio più in là, e a due passi dalla ferrovia interna del petrolchimico dove arrivano cisterne di monomeri e di titanio tetracloruro, c'è il laboratorio analisi di controllo, uno scrigno di macchinari e tecnologia dove 80 camici bianchi mappano l'infinitesimale tra cromatografie, spettrometrie di massa e fluorescenza a raggi x dei materiali finiti. Controlli degni della scientifica anche se si tratta di prendere le impronte a una vaschetta di prosciutto o alla confezione dell'ovetto Kinder. «Qui supportiamo anche gli impianti del resto di Europa e si lavora sempre in stretta sinergia con le imprese clienti, da Unilever a Fiat», precisa il responsabile R&D del centro Natta, Gabriele Mei, snocciolando numeri e nomi delle innovazioni che hanno preso vita a Ferrara nei decenni. Tecnologie vendute worldwide come le 110 licenze Spheripol, lo Spherizone o il processo Catalloy e l'ultima novità 2012, i catalizzatori senza ftalati.
Permalink
Ultimi di sezione
Dai nostri archivi
Moved Permanently
The document has moved here.