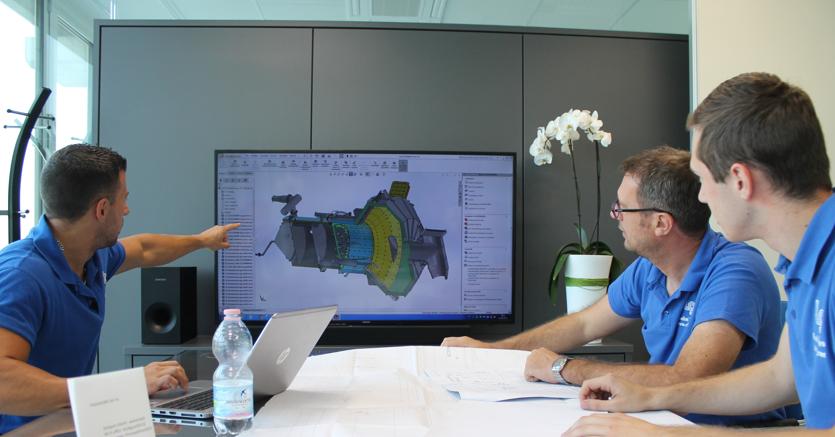
«Dicevano: vedrete che falliranno, hanno fatto il passo più lungo della gamba». E invece no. Miriam Gualini è alla guida dell’azienda di famiglia, ancora in pista nonostante la sfiducia dei concorrenti dopo quel maxi-acquisto del 1995, uno dei laser industriali da carpenteria più grandi d’Europa (due miliardi di lire investiti), certo non uno standard per una Pmi che a quei tempi fatturava una manciata di miliardi delle vecchie lire. E tuttavia, la storia di Gualini Lamiere International di Bolgare (Bergamo), 60 addetti impegnati in lavori di carpenteria pesante, dimostra che investimenti e upgrade dei processi non siano appannaggio esclusivo delle grandi aziende. E i percorsi 4.0 non fanno eccezione. «Siamo partiti in realtà già tre anni fa - spiega l’ad - acquistando macchine connesse per il controllo dei processi produttivi. Abbiamo investito moltissimo ma non ci siamo fermati».
La disponibilità dei dati è un primo mattone su cui Gualini ha costruito molto altro, digitalizzando ad esempio la logistica. «Per noi un processo cruciale - aggiunge - perché ogni anno dobbiamo movimentare 18mila tonnellate di materiale, da pezzi di pochi chili ad altri enormi. E se sbagli posizione in magazzino puoi anche perdere ore per ricollocare il pezzo nel modo corretto». L’upgrade logistico è stato effettuato dotando ciascun prodotto di un bar code, mentre in parallelo l’intera area aziendale veniva mappata e suddivisa in celle di carico e scarico. Gli operatori, dotati di un mini-computer da polso, possono così dialogare in tempo reale con il sistema logistico per effettuare le missioni di spostamento, minimizzando errori e ritardi. «I risultati sono stati evidenti - spiega l’imprenditrice - perché se guardiamo al nuovo assetto della nostra logistica vediamo una produttività cresciuta nell’ordine del 30%: a parità di personale ora siamo molto più rapidi e precisi».
Anche i processi produttivi sono stati interessati dalla digitalizzazione, grazie all’utilizzo di una rete wi-fi per far “parlare” l’ufficio di programmazione con i reparti. «L’operazione più delicata per noi è la saldatura - aggiunge - e grazie al dialogo tra i sistemi riusciamo a migliorare la qualità finale». L’interconnessione è ad esempio vitale nei momenti di cambio-turno (in azienda sono tre), consentendo all’operatore subentrante di procedere nel lavoro usando gli stessi parametri del collega che termina il proprio orario. Mentre le eventuali saldature anomale sono bloccate da un sistema di allarme, evitando così che il difetto proceda lungo il processo. I dati, inoltre, sono registrati e accoppiati al prodotto, lo seguiranno nel book di certificazione consegnato al cliente.
«Per restare competitivo devi innovare - aggiunge l’ad - e noi non ci fermiamo. Insieme all’università di Modena e Reggio Emilia e al consorzio Intellimech di cui facciamo parte, ad esempio, stiamo studiando come inserire robot collaborativi in saldatura. Macchine che imparino dai movimenti umani per poi procedere in autonomia».
© Riproduzione riservata