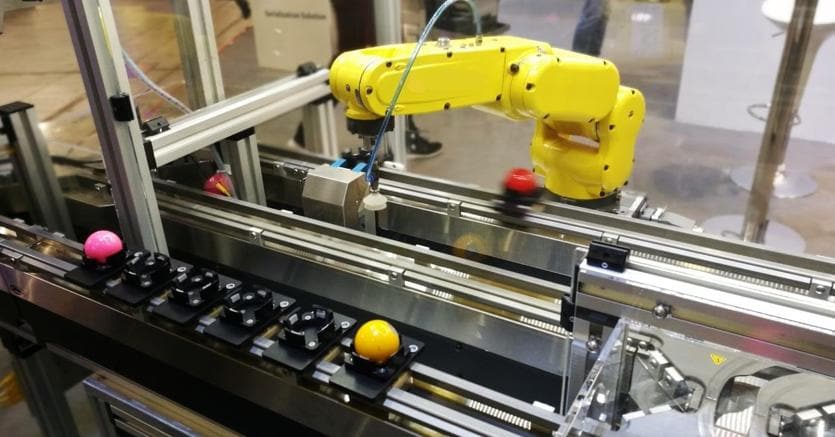
Al cambio del turno arriva un nuovo saldatore. Che a differenza del passato non deve più andare per tentativi o chiedere al collega: è la rete wi-fi a impostare l’attrezzo con i parametri corretti, blindando in un range predefinito tensione, corrente, potenza e avanzamento del filo.
Piccola-grande svolta, quella realizzata da Gualini Lamiere, Pmi bergamasca da 20 milioni di ricavi che ha imboccato con decisione la strada della digitalizzazione. Inserendo tecnologie 4.0 in un mondo, quello della carpenteria pesante, che pare distante anni luce da codici binari, algoritmi e big data. Non è così. E grazie all’innovazione è ora possibile non solo uniformare la qualità dei prodotti ma anche tenere traccia di ogni variabile produttiva, aumentando il valore aggiunto di ciò che viene fornito al cliente. «E tutto questo - sintetizza l’imprenditrice Miriam Gualini - alla fine si traduce in maggiore competitività».
Potenza della “connessione”, capacità di produzione e condivisione dei dati ormai entrata a gamba tesa nella vita delle aziende di ogni dimensione, imprese reduci da un biennio forse irripetibile di investimenti in nuovi macchinari. Scatto in grado di portare il consumo nazionale di settore al nuovo massimo storico, 26,5 miliardi, oltre il periodo pre-crisi, grazie ad un salto in avanti del 10% nel 2018 che ha bissato l’analogo passo in avanti realizzato l’anno precedente.
Investimenti che progressivamente cambiano le modalità operative delle aziende, dando loro la possibilità di creare processi che si autoregolano, attraverso macchine che entro certi limiti sono in grado di modificare in autonomia il proprio funzionamento sulla base dei dati raccolti. Accade ad esempio a Bologna in Marchesini (macchinari per packaging, 400 milioni di ricavi), che ha da poco realizzato una linea di produzione blister in grado di utilizzare le informazioni raccolte per migliorare la qualità del processo correggendo errori in via preventiva, individuando le cause dei cali di produzione, anticipando le operazioni di manutenzione di routine.
Scelta in un certo senso obbligata quella dei costruttori di beni strumentali, perché la domanda di mercato ormai va pesantemente in quella direzione, sia per effetto degli incentivi fiscali ancora vigenti, sia per la volontà delle imprese di spingere l’acceleratore su efficienza e competitività. Il nuovo impianto bergamasco di Fassi (gru), investimento da 20 milioni, è interamente costruito con questa logica. Inserendo macchine con asservimenti automatici, carrelli agv per la logistica, impianti in grado di gestire in modo flessibile più lavorazioni. «Produciamo migliaia di codici - spiega l’ad Giovanni Fassi - e l’obiettivo che ci siamo posti è quello di realizzare in modo efficiente anche il singolo pezzo, il lotto “uno”. Alcune fasi che in passato erano gestite in termini manuali ora sono automatizzate, mentre cresce l’attività nell’area di programmazione e gestione dei dati».
In parallelo nel Paese si diffonde anche l’automazione per eccellenza, la robotica. Trend dirompente che spinge a nuovi investimenti i colossi del settore: Fanuc, ad esempio, ha appena raddoppiato il proprio quartier generale alle porte di Milano, investendo 20 milioni di euro.
Il consumo di robot lo scorso anno è arrivato in Italia al nuovo record storico, a 9.237 unità, in crescita dell’11,5% rispetto all’anno precedente, più che doppiando i livelli pre-crisi e realizzando una performance nettamente superiore rispetto alla crescita media mondiale, limitata a un punto percentuale.
«Trend che prosegue - spiega il presidente di Siri, associazione italiana di robotica e automazione, Domenico Appendino - perché dalle stime che abbiamo, a fine anno si potrebbe arrivare attorno a 9.700 unità, realizzando una crescita del 5%. Del resto, anche se con qualche modifica, l’impianto complessivo degli incentivi legati a Industria 4.0 è stato confermato».
Crescente è anche la diffusione di strumenti ibridi, dagli esoscheletri, piccole “armature” indossabili in grado di alleviare gli sforzi di sollevamento (numerose aziende stanno già testando quelli di Comau) ai robot collaborativi, macchine in grado di stare a contatto con gli operatori di linea. Nicchia per ora limitata (si stimano nel 2018 400-450 applicazioni) ma che esprime tassi di crescita nell’ordine del 50 per cento. «L’Italia può solo trarre vantaggi da questa situazione - aggiunge Appendino - perché in questo modo si riduce l’impatto del costo del lavoro, ponendo le basi per un reshoring di attività. Grazie ai robot è possibile migliorare la competitività delle aziende e quindi del Paese».
Tutto bene? In realtà il percorso delle aziende è solo avviato, come dimostra l’ultima ricerca Bcg-Ipsos realizzata su un campione di 170 aziende manifatturiere. Il 22% di queste ammette di non aver avviato e neppure pianificato alcun progetto di digitalizzazione. Del 78% che invece è già “partito”, solo un quarto realizza progetti pervasivi ad elevata complessità, in grado di impattare pesantemente sull’intera catena del valore, dal fornitore fino al cliente finale.
© Riproduzione riservata