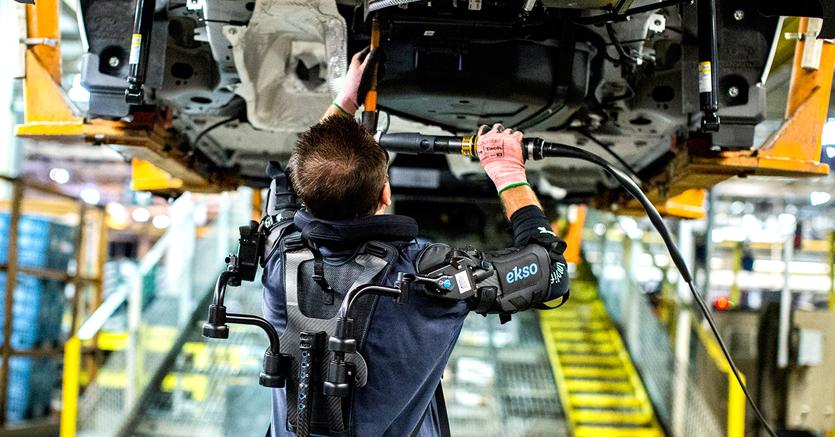
Fatta l’industria 4.0, bisogna fare i suoi lavoratori: operai, tecnici e manager 4.0. Ogni rivoluzione industriale ha richiesto, per dare frutti, anche una mutazione della forza lavoro e del suo modo di pensare l’azienda, di partecipare alla produzione, di immaginare beni e servizi.
Circa 120 anni fa, le fabbriche americane iniziarono a elettrificare le proprie linee di produzione, contribuendo al compimento della seconda rivoluzione industriale. In quelle fabbriche, però, la produzione non crebbe per i successivi 30 anni. Un tempo sufficiente affinché i dirigenti che avevano introdotto quell’innovazione andassero in pensione. Quelle persone avevano sostituito le macchine a vapore con dei motori elettrici, ma non avevano riorganizzato le fabbriche per sfruttare i vantaggi dell’elettricità.
Nell’industria 4.0 la digitalizzazione diffusa ha preso il posto dell’elettrificazione, con la completa integrazione delle tecnologie informatiche con tutti i processi economici e produttivi. La spinta del “digital inside” sta causando una mutazione della forza lavoro.
L’essere umano è passato dal pensare di dover competere contro le macchine a scoprire di poter competere insieme alle macchine. I robot industriali hanno sostituito l’uomo nelle attività più faticose ma ora quelli collaborativi, progettati per lavorare fuori dalle “gabbie” di sicurezza, hanno iniziato ad affiancare gli operai sulle linee di produzione: possono fare moltissimo, ma hanno bisogno dell'uomo. I robot sono diventati i migliori compagni dei lavoratori. E con l'arrivo della generazione degli esoscheletri robot, l'operaio 4.0 è chiamato a indossarli, con la stessa facilità con cui indossa un vestito.
La Chairless chair (letteramente: “sedia senza sedia”) progettata dalla startup Svizzera Noonee è stata adottata da Audi: è un robot-esoscheletro che si infila come un pantalone e sostiene i lavoratori in posizione semi eretta, riducendo l'affaticamento agli arti inferiori senza limitare i movimenti del lavoratore. Ford e Fca hanno sviluppato, per vie indipendenti, esoscheletri per gli arti superiori, che aiutano l'operaio a sollevare pezzi o utensili con peso da pochi grammi fino a 60 kg, senza il minimo sforzo. Hynday ha testato un esoscheletro completo, mutuato dalla piattaforma H-LEX (Hyundai Lifecaring Exoscheltron): un “costume di metallo” – tra i più leggeri della sua categoria – che assiste sia gli arti inferiori che quelli superiori per sollevare pesi di oltre 100 kg. Molto simile al Power Loader, l'esoscheletro che Panasonic ha già messo in produzione dotato di 4 sensori per mani e piedi e 20 servomotori. Anche la comunità robotica italiana è al lavoro con Iuvo, società spin-off dell'Istituto di Bio Robotica della Scuola Sant'Anna di Pisa in cui hanno investito anche Comau (l'azienda torinese è socio di maggioranza) e la società islandese di bioingegneria Ossur, specializzata in protesi hi-tech. Fondata nel 2015, Iuvo – che sfrutta le competenze in tecnologie robotiche indossabili dei ricercatori della Sant'Anna – progetta esoscheletri pensati per applicazioni in ambito manifatturiero, ma non solo.
Oltre alla forza, le tecnologie dell'industria 4.0 aumenteranno anche i sensi dei lavoratori. Dalla vista al tatto. Volvocars, per esempio, da tempo lavora con Microsoft per l'utilizzo degli HoloLens – gli occhiali che, se indossati, proiettano informazioni o oggetti sotto forma di ologrammi – sia nelle linee di produzione che negli autosaloni. Anche Iveco Bus sta testando lo stesso dispositivo, sperando di poterlo sfruttare nella manutenzione da remoto. Mentre il gruppo Daimler, nella sua TecFabrik, utilizza sensori indossabili per catturare i movimenti del tecnico specializzato e riprodurli in un ambiente virtuale. Il lavoratore viene “immerso” in un simulatore di realtà e può, per esempio, utilizzare una stazione di montaggio e verificarne l'efficienza, senza che questa sia stata costruita fisicamente.
La quarta rivoluzione industriale non riguarda solo la manifattura o l'operaio in tuta blu. Un esempio dal mondo dei servizi è appena nato in Italia. I già citati HoloLens di Microsoft sono utilizzati quotidianamente dai consulenti finanziari di Widiba, la banca multicanale del gruppo Mps in due uffici di Siena e Milano. I bancari 4.0 ascoltano il cliente mentre gli occhiali proiettano davanti a loro informazioni sulla sua propensione al rischio, o su eventuali investimenti già attivi. Mentre un robo advisor dotato di intelligenza artificiale assiste il consulente nell'elaborazione della proposta di investimento.
Per maneggiare attrezzi così potenti, servono però nuove competenze. “La parola d'ordine – conferma Giuliano Busetto, responsabile della divisione digital factory e process industries and drives di Siemens Italia – è “contaminazione”, sia in senso verticale che orizzontale. Dovranno essere create e formate delle figure cross disciplinari in grado di coniugare l'innovazione tecnologica con la realtà e la specificità organizzativa della singola realtà industriale”.
La Commissione europea ha calcolato che entro il 2020 il mercato richiederà 800mila professionisti del digitale. E che l'offerta non soddisferà la domanda se non in minima parte, soprattutto perché, stima sempre la Commissione, oggi il 40% della forza lavoro europea non ha le competenze digitali di base. La trasformazione culturale richiesta ai lavoratori dall'Industria 4.0 è più profonda e complessa rispetto a quella fisica. Non sarà facile come indossare un esoscheletro.
© Riproduzione riservata