Storia dell'articolo
Chiudi
Questo articolo è stato pubblicato il 15 dicembre 2013 alle ore 08:42.
L'ultima modifica è del 19 giugno 2014 alle ore 11:10.
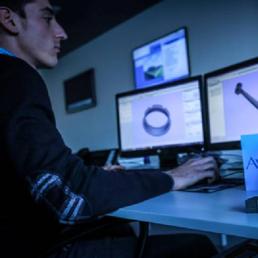
Dalla polvere al prodotto finito. Nasce in provincia di Novara, nel cuore del Nord manifatturiero, uno degli stabilimenti più innovativi al mondo nella produzione di componenti (pale e turbine) per motori di aerei ed elicotteri civili e militari. È il nuovo impianto di Avio Aero, società controllata al 100% da General Electric, inaugurato ieri a Càmeri alla presenza del ministro dello Sviluppo, Flavio Zanonato.
«Questo stabilimento – dice il ministro – è un esempio di come il Paese può risollevarsi. In un momento di grande crisi è un segnale importante».
Con l'impianto di Cameri, Avio Aero dimostra efficacemente il significato del «fare industria investendo nelle tecnologie nascenti»: nello specifico nell'additive manufacturing. Questa tecnologia, nota come stampa 3D, consente di realizzare, partendo da un modello digitale, oggetti solidi di qualunque forma attraverso l'aggregazione di polveri di speciali leghe metalliche. Nel nostro caso stiamo parlando di pale turbine per jet in alluminio di titanio con prestazioni termodinamiche equivalenti ai materiali convenzionali, ma con peso ridotto del 50 per cento. «Pale turbine più leggere destinate ai motori aeronautici del futuro, motori performanti a basse emissioni» spiegano gli ingegneri di Avio Aero. Con i suoi 2.500 metri quadrati, lo stabilimento piemontese è uno dei più grandi al mondo per la produzione in 3D. Questa tecnologia in particolare risponde appieno alle principali sfide dell'industria aeronautica: la riduzione dei pesi e la riduzione dei tempi di produzione dei componenti, che utilizzano leghe metalliche sempre più innovative e resistenti. Produrre un iniettore combustore di un motore aeronautico con la tecnologia tradizionale comporta saldare componenti realizzati separatamente partendo da microfusioni, mentre con la tecnologia additive l'iniettore viene realizzato direttamente in un unico pezzo. La produzione in 3D consiste proprio nel mettere assieme dei pezzi partendo da polveri dei metalli di base e fuse insieme, uno strato dopo l'altro, da un fascio di luce laser o di elettroni. Rispetto alle tecnologie tradizionali che impiegano in media quattro chilogrammi di materia prima per un chilo di prodotto finito, la nuova tecnologia consente l'impiego di appena 1,1 chilogrammi di materia prima. Con un taglio del 95% dei materiali, del 90% delle energie, del 90% dei gas serra.
L'impegno di Avio Aero a crescere spingendo sulla leva dell'innovazione è stato consistente negli anni: tra il 2010 e il 2012 l'azienda ha investito nel business aeronautico circa 400 milioni di euro e di questi 100 milioni sono stati destinati all'attività di ricerca e sviluppo. Nello specifico, l'investimento nella tecnologia additive manufacturing, incluso il nuovo stabilimento di Cameri, si aggira sui 20 milioni negli ultimi quattro anni. È il coronamento di un percorso iniziato nel 2007, spiegano i dirigenti della Avio Aero, con l'accordo siglato con una piccola azienda novarese, la Protocast specializzata in questa tecnologia e poi assorbita e sviluppata da Avio.
«Per restituire competitività al nostro sistema produttivo – sottolinea Zanonato – dobbiamo mettere sempre più al centro competenze e innovazione tecnologica. Solo combinando innovazione e ricerca potremo guardare al futuro con maggiore ottimismo e lasciarci alle spalle le difficoltà della crisi».